THE Rotary Indexing Machine
Walk into any high-volume aerosol manufacturing plant, and you’ll likely see a rotary indexing machine quietly driving the rhythm of production. Though it may not get the spotlight, this piece of equipment is central to making sure products like deodorants, air fresheners, and industrial sprays get filled, sealed, and packaged with consistency and speed.
At a glance, it’s a circular setup—stations positioned like the numbers on a clock. Each canister takes a ride around this loop, stopping briefly at designated points for tasks like filling, crimping, labeling, or even checking for defects. It’s the type of automation that doesn’t just improve efficiency—it defines it.
But here’s the thing: while the machine itself is impressive, how it’s configured and maintained often makes or breaks its value on the production floor.
Key Takeaways
- The Aerosol Rotary Indexing Machine is a key component in aerosol production, allowing for efficient filling, sealing, and labeling of aerosol cans.
- Setting up the Aerosol Rotary Indexing Machine for optimal efficiency involves proper calibration, maintenance of components, and regular inspection to ensure smooth operation.
- Maximizing production output with the Aerosol Rotary Indexing Machine requires careful planning of production schedules, efficient use of resources, and minimizing downtime through proactive maintenance.
- Ensuring quality control in aerosol production with the Rotary Indexing Machine involves regular testing of filled cans, monitoring of machine performance, and adherence to strict production standards.
Setup: More Than Just Aerosol Plug and Play
Setting up one of these machines isn’t as simple as flipping a switch. It begins with understanding the specific needs of your product—what size cans are you using? How thick is the liquid? Do you need to fill at high speed or prioritize accuracy?
Each of those questions leads to adjustments: fill volume settings, nozzle positioning, sealing pressure, rotation speed, and so on. Misalign just one component and you could end up with underfilled cans, product leaks, or unnecessary slowdowns.
In practice, most experienced operators know it takes a few test runs, some fine-tuning, and a trained eye to get things humming. And yes—training matters. A well-set machine is only as good as the people running it.
Getting More Out of Your Rotary Indexing Assembly Machine
Once the setup’s dialed in, the focus shifts to optimization. You want speed, of course, but not at the expense of quality. Cranking up the RPM might boost your unit count for the hour, but if 5% of them need to be pulled for rework, you’ve gained nothing.
This is where smart monitoring tools can be game-changers. Think sensors tracking fill levels, cycle times, and valve performance. Or real-time dashboards that flag inconsistencies before they become problems. Many facilities now use data analytics not just for fixing problems—but for preventing them in the first place.
Another often overlooked trick? Automating tasks around the machine. Things like labeling, boxing, or weighing can be integrated to create a seamless production flow that keeps people focused on what truly needs attention.
Quality Control: It’s Not Just Simply Checking A Box
Metrics | Value |
---|---|
Production Output | 5000 units per hour |
Defect Rate | 0.5% |
Machine Downtime | 2 hours per week |
Quality Control Checks | Every 30 minutes |
Operator Training Hours | 40 hours per operator |
In aerosol production, small mistakes can lead to big consequences. A leaking can or a misfire isn’t just an annoyance—it can damage brand trust or even cause safety issues.
That’s why good manufacturers build quality control into every step. Some do manual spot checks every 15 or 30 minutes. Others rely on camera systems that scan for label placement, seal integrity, or even spray pressure.
But technology isn’t a total replacement for judgment. Many of the best quality checks come from operators who know what “right” looks like—and feel confident to flag what doesn’t.
Documentation helps here too. Standard operating procedures (SOPs) that outline inspection steps, tolerance levels, and corrective actions help keep everyone on the same page, regardless of shift.
Maintenance: The Real Key to Longevity
Machines like these will run hard—but only if you take care of them. Bearings need grease. Fill lines need cleaning. Belts wear out, sensors drift. It’s all part of the job.
Most facilities use a maintenance schedule to stay ahead of issues, but the best ones go a step further: they train operators to spot early signs of trouble. A subtle sound change or a slightly off timing sequence might not seem like much—but it’s often the first warning sign of a bigger problem.
When issues do pop up, having a simple, well-documented troubleshooting guide can make the difference between a 10-minute fix and a full-hour delay. And when it’s beyond in-house capabilities, don’t hesitate to call in a tech from the machine manufacturer—downtime isn’t cheap.
Final Thoughts
The aerosol rotary indexing machine might not be flashy, but it’s one of those unsung heroes of modern manufacturing. It turns what could be a chaotic, multi-step process into a clean, repeatable system. But like any tool, its success depends on how well it’s set up, maintained, and monitored.
In the end, it’s not just about the machine—it’s about the team around it, the data supporting it, and the culture that values doing things right the first time.
More Articles of Interest:
FAQs
What is an aerosol rotary indexing machine?
An rotary indexing assembly machine is a type of packaging machinery used in the production of aerosol products. It is designed to automatically fill, seal, and package aerosol cans in a high-speed, efficient manner.
How does an aerosol rotary indexing machine work?
An aerosol rotary indexing machine works by using a rotating indexing system to move aerosol cans through various stations, including filling, valve placing, crimping, and propellant filling. Each station is equipped with specialized equipment to perform the necessary tasks, such as filling the cans with product, sealing the cans, and adding propellant.
What are the benefits of using an aerosol rotary indexing machine?
Some of the benefits of using an aerosol rotary indexing machine include increased production speed, improved efficiency, consistent and accurate filling and sealing of aerosol cans, and reduced labor costs. These machines are also designed to meet industry standards for safety and quality control.
What industries use aerosol rotary indexing machines?
Aerosol rotary indexing machines are commonly used in industries such as pharmaceuticals, personal care products, household chemicals, automotive products, and industrial applications. These machines are versatile and can be used to package a wide range of aerosol products.
What factors should be considered when choosing an aerosol rotary indexing machine?
When choosing an aerosol rotary indexing machine, factors to consider include production capacity, the size and type of aerosol cans to be filled, the level of automation required, and the specific requirements of the product being packaged. It is also important to consider the reputation and support services of the manufacturer.
How To Choose Bag On Valve ManufacturerS
If you’re manufacturing top-quality products that need safe, clean, and efficient dispensing (like personal care sprays, food-grade aerosols, or even pharmaceutical solutions), Bag On Valve (BOV) technology might be exactly what you need.
But choosing the right BOV manufacturer requires some thought and consideration.
Other Articles You Might Be Interested In:
- What is Bag-On-Valve Aerosol?
- How To Choose Aerosol Filling Companies?
- What is Bag On Valve (BOV) Aerosol Filling?
Before we look into how to choose a manufacturing partner, let’s summarize what Bag-On-Valve actually is, and why it’s is used so frequently.
So, What is Bag-On-Valve?
Bag-On-Valve is a clever bit of packaging innovation. Imagine your product—say, a skincare serum or a nasal spray—sealed inside a bag, which is then tucked inside a pressurized can. When you press the valve, the product gets dispensed by air or nitrogen pushing on the outside of the bag—not mixing with the product at all.
The result? A more hygienic, longer-lasting product that feels luxurious and effortless to use.
Why More Brands Are Choosing BOV
Let’s talk benefits—because BOV delivers on multiple fronts:
- 360° dispensing: Want your product to work upside down, sideways, or in any position? BOV’s got you covered.
- Longer shelf life: Since there’s no contact with air or propellants, your formulas stay fresher, longer.
- Eco-friendlier: Many BOV systems use clean air or nitrogen instead of chemical propellants.
- No contamination: The product stays completely sealed off from outside elements.
- Versatile applications: From medical sprays to food products, BOV is used across a wide range of industries.
What to Look for in Bag On Valve Manufacturers
Not all manufacturers are created equal. Here are the key qualities that separate a reliable BOV partner from the rest:
✅ Quality & Certifications
Make sure they meet global standards—think FDA, ISO, and other regulatory boxes that need ticking, depending on your market.
🛠️ Customization Capabilities
Whether you need specific can sizes, valves, or filling specs, a good partner should tailor their systems to your product—not the other way around.
🏭 Production Power
Can they scale with you? If your order volume grows, your manufacturer should be ready to keep up without compromising on lead times.
💡 Innovation & R&D
The best partners don’t just manufacture—they collaborate. Look for companies investing in tech, testing, and continuous improvement.
🌍 Sustainability Mindset
Green is no longer a niche. Today’s consumers care, and your manufacturer should too. Eco-friendly processes and recyclable components go a long way.
Why Terco Should Be on Your Radar
If you’re serious about quality and long-term success, Terco is a name worth knowing. With decades in the aerosol and BOV space, they bring deep expertise—and a global footprint—to the table.
Here’s why they stand out:
🌐 Worldwide Reach, Small-Batch Attention
Terco serves clients across the globe but still offers the hands-on service of a boutique manufacturer. You’re not just a number—you’re a partner.
♻️ Sustainability as a Standard
They’re not playing catch-up on green practices—they’ve been ahead of the curve. Terco’s systems support recyclable packaging and eco-conscious production from the ground up.
🧰 On-Site Service & Full Support
Need help with installation, training, or troubleshooting? Terco’s team shows up—literally. They offer full on-site service to keep your production lines humming.
🔧 All the Parts, All the Time
No more hunting down rare components or worrying about downtime. Terco ensures full parts availability for every machine they’ve ever made.
In summary:
Choosing Bag On Valve manufacturers isn’t just a box to check—it’s a strategic decision that affects your product’s performance, shelf life, sustainability, and even your brand perception. If you’re looking for a partner that combines innovation, reliability, and real-world expertise, Terco checks every box.
Spray Can Filler Machine
We carry a full line of equipment, parts and supplies to allow you to fill your own aerosol cans. Our systems have been designed, built, and tested for many years, and are designed to fill anywhere from a few cans to more than 100 cans/hour. We’ll help you pick the system that is right for you!
The spray can filler machine is especially important for goods that need aerosol delivery systems. These devices are made to fill aerosol cans with a range of materials, such as paints, lubricants, cleaning supplies, & personal hygiene items. Ensuring customer satisfaction & upholding quality control depend heavily on the ability to precisely and efficiently fill cans with a constant volume of product. Spray can filler technology has advanced significantly as a result of the need for dependable and effective filling solutions as industries continue to change.ge.
Key Takeaways
- Spray can filler machines are used to fill aerosol cans with various products such as paints, adhesives, and personal care products.
- Using a spray can filler machine can increase production efficiency, reduce labor costs, and improve product quality.
- Spray can filler machines work by using a pressurized system to fill cans with product, and can be customized for different can sizes and product viscosities.
- Spray can filler machines are used in a wide range of industries including automotive, household, and personal care products.
- Advancements in spray can filler machine technology include improved automation, faster filling speeds, and enhanced safety features, leading to increased productivity and reduced downtime.
Aerosol can filling was a time-consuming & frequently error-prone procedure in the past. Inconsistencies in product volume caused by manual filling techniques could have an impact on the finished product’s quality as well as raise waste and production expenses. This procedure was transformed with the advent of automated spray can filler machines, which enabled producers to increase accuracy and productivity. Advanced features on these machines simplify the filling process, lower labor costs, and increase overall productivity.
Enhanced Production Effectiveness. A major advantage of using a spray can filler machine is the notable boost in production efficiency. Compared to manual methods, automated systems can fill cans much more quickly—often hundreds of cans per minute. Because of this quick filling capacity, producers can satisfy strong demand without sacrificing quality.
greater consistency and a decrease in human error. Also, the automation guarantees that every can is consistently filled to the proper volume, lowering the possibility of human error. This constancy is essential for preserving product quality and cutting down on waste. Flexibility and Adaptation. The adaptability of spray can filler machines is another benefit.
Metrics | Data |
---|---|
Filler Machine Capacity | 1000 cans/hour |
Accuracy | ±0.5% |
Energy Consumption | 10 kW |
Material Compatibility | Various types of spray can materials |
From fine powders to viscous liquids, they can be modified to work with a variety of products. Because of their adaptability, they can be used in a variety of sectors, such as the automotive, cosmetic, and household cleaning industries. Also, a lot of contemporary machinery has movable settings that let users quickly switch between various product kinds and can sizes, which makes it simpler for producers to expand their product lines without having to buy several specialized machines. The precise filling and appropriate sealing of aerosol cans are ensured by a number of crucial steps in the operation of a spray can filler machine.
The machine is initially fed empty cans through a conveyor system. After the cans are in place, the machine secures them there using a combination of mechanical arms and sensors. This guarantees that every can is properly positioned for filling, which is essential for accuracy.
A nozzle that dispenses the product into the can is usually used for filling. Different filling mechanisms may be used depending on the kind of product being filled. For example, a volumetric filling system may be used for liquid products, which measures out a predetermined amount before dispensed into the can. Products that need to be pressurized, on the other hand, might make use of a pressure filling system that enables the addition of propellant gases to the product.
In order to maintain their airtightness and distribution readiness, the cans are sealed with a cap or valve after filling. Because they can handle a wide variety of products, spray can filler machines find use in a wide range of industries. These devices are frequently used in the automotive industry to fill cans with paints, lubricants, and sprays intended for auto maintenance & repairs. These machines’ accuracy guarantees that automotive products are dispensed precisely, which is essential for both performance and safety. Spray can fillers are used in the personal care industry to package hair sprays, deodorants, & other cosmetics.
Cans can be filled with a variety of formulations, such as oil-based sprays or alcohol-based solutions, showcasing the machines’ versatility. Also, spray can fillers are commonly used in the packaging of household cleaning products like air fresheners and disinfectants, enabling manufacturers to satisfy consumer demand for easy-to-use & efficient cleaning solutions. The main goals of recent developments in spray can filler machine technology have been to increase productivity, precision, and user-friendliness.
Smart technology’s incorporation into these devices is one noteworthy advancement. A lot of contemporary spray can fillers come with sensors and software that track the filling operation in real time. Manufacturers can reduce downtime and increase overall productivity by using this data-driven approach to identify possible problems before they become more serious. Also, spray can filler machines now have stronger parts thanks to developments in materials science. Over time, these upgrades lower maintenance costs while also increasing the equipment’s lifespan.
Also, manufacturers can now switch between product lines with little downtime thanks to innovations like quick-changeover systems, which further improve operational efficiency. Spray can filler machines seem to have a bright future as long as businesses keep looking for packaging solutions that are more sustainable and effective. An emerging trend that is likely to influence this future is the growing focus on environmentally friendly practices. By using recyclable materials and creating refillable aerosol systems, manufacturers are attempting to minimize their environmental impact and reduce waste. For spray can filler machines to remain effective, they will need to change to fit these new packaging formats.
Also, spray can filler machines are likely to integrate increasingly sophisticated robotics and artificial intelligence capabilities as automation spreads throughout a variety of industries. More accurate filling procedures and the smooth handling of increasingly complicated product formulations are made possible by these technologies. The incorporation of machine learning algorithms may also result in predictive maintenance capabilities, whereby devices use historical data to predict failures before they happen. In summary, spray can filler machines will become more and more important in satisfying consumer demands for efficiency and sustainability as industries change and consumer preferences change.
Not only will they perform better thanks to continuous technological advancements, but they will also continue to play a crucial role in packaging for years to come.
If you are interested in learning more about aerosol cans, you may want to check out this article on bag-on-valve aerosol cans versus traditional aerosol cans. This article discusses the differences between the two types of aerosol cans and the benefits of using bag-on-valve technology. It provides valuable insights into the advantages of this innovative packaging solution for various industries.
FAQs
What is a spray can filler machine?
A spray can filler machine is a piece of equipment used in the manufacturing process of aerosol spray cans. It is designed to fill empty cans with the desired product, such as paint, lubricant, or air freshener, and then seal the cans with a valve and cap.
How does a spray can filler machine work?
A spray can filler machine works by first placing empty cans onto a conveyor belt or rotary table. The cans are then filled with the product using a precise metering system. Once filled, the cans are moved to a sealing station where a valve and cap are applied to complete the process.
What are the benefits of using a spray can filler machine?
Using a spray can filler machine offers several benefits, including increased efficiency in the filling and sealing process, improved accuracy in product measurement, and reduced labor costs. Additionally, these machines can handle a wide range of can sizes and product viscosities.
What industries use spray can filler machines?
Spray can filler machines are commonly used in industries such as automotive, household chemicals, personal care products, and industrial manufacturing. These machines are versatile and can be adapted to fill a variety of products into aerosol cans.
Are there different types of spray can filler machines?
Yes, there are different types of spray can filler machines available, including semi-automatic and fully automatic models. Semi-automatic machines require some manual intervention, while fully automatic machines can operate with minimal human oversight. Additionally, there are different filling technologies, such as volumetric or gravimetric, to accommodate various product types.
Efficient Aerosol Filling Equipment for Your Production Needs
Having a thorough understanding of aerosol filling equipment is essential to the manufacturing of aerosol products, which are utilized extensively in a variety of sectors, such as the automotive, household cleaning, & personal care industries. Fundamentally, the purpose of aerosol filling equipment is to fill pressurized containers with liquids or semi-liquids, which are subsequently released as a fine mist or spray. With the introduction of cutting-edge features that improve productivity, security, and product quality, this technology has undergone substantial development over time.
Key Takeaways
- Aerosol filling equipment is used to fill aerosol products such as sprays, foams, and gels into containers under pressure.
- When choosing aerosol filling equipment, factors to consider include production capacity, container size, and product viscosity.
- Efficient aerosol filling equipment can lead to increased productivity, reduced waste, and improved product quality.
- Types of aerosol filling equipment include semi-automatic and automatic filling machines, as well as propellant filling machines.
- Maintenance and safety considerations for aerosol filling equipment include regular cleaning, inspection of valves and seals, and proper training for operators.
- To optimize production with efficient aerosol filling equipment, consider automation, quality control measures, and regular equipment maintenance.
Manufacturers looking to streamline their production processes must comprehend the complexities of this machinery. Filling machines, propellant systems, & capping mechanisms are usually the fundamental parts of aerosol filling apparatus. While the propellant system makes sure the contents are pressurized for efficient dispensing, the filling machine is in charge of precisely dispense the product into the canister. To keep the product intact and stop leaks, the capping mechanism closes the canister.
As we learn more about aerosol filling, we see that equipment selection has a big influence on production efficiency, output quality, and cost. Considerations for Selecting Aerosol Filling Equipment A number of factors are taken into account when choosing aerosol filling equipment, and these factors may affect our choice. The kind of product that is being filled is one of the main factors. Certain equipment configurations or filling methods may be needed for particular products. For example, thicker formulations might require specific nozzles or pumps to guarantee constant filling without clogging. Determining the best equipment requires an understanding of our product’s features.
Production capacity is an additional important consideration. In order to select equipment that can satisfy our demands without sacrificing efficiency, we must evaluate our present and future production needs. This entails assessing the system’s overall throughput, the filling process’ speed, and the quantity of canisters filled per minute. The equipment’s adaptability to various canister sizes and shapes should also be taken into account, as this can improve our capacity to react to shifts in the market and consumer preferences.
Features | Benefits |
---|---|
High filling accuracy | Ensures precise and consistent filling of aerosol products |
Fast filling speed | Increases production efficiency and output |
Easy integration with production line | Minimizes downtime and streamlines production process |
Low maintenance requirements | Reduces operational costs and downtime for maintenance |
Compliance with industry standards | Ensures product quality and regulatory compliance |
Efficient Aerosol Filling Equipment Benefits Purchasing efficient aerosol filling equipment can greatly increase our production capacity and offer a number of advantages. Increased productivity is among the most obvious benefits. By operating at high speeds without sacrificing accuracy, modern filling machines enable us to fill more canisters in less time. Our output is increased by this efficiency, which also enables us to meet deadlines & promptly address client requests. Also, effective aerosol filling machinery enhances the quality of the final product. By guaranteeing accurate filling volumes, advanced technology lowers the possibility of canisters being overfilled or underfilled.
Delivering products consistently improves customer satisfaction and reduces waste, which eventually lowers costs. Also, a lot of contemporary equipment has quality control features that track the filling process in real time, enabling us to quickly detect & address any problems. The market provides a wide variety of aerosol filling equipment designed to satisfy different production requirements. A popular kind that offers flexibility for smaller production runs but necessitates some manual intervention is the semi-automatic filling machine. Businesses that want accuracy & efficiency in their filling procedures but may not have high volume requirements are best suited for these machines.
Conversely, completely automated aerosol filling machines are made for production settings with large volumes. These devices use cutting-edge automation technologies to operate continuously with little assistance from humans. Frequently, they have advanced control systems that oversee all filling operations, including product dispensing, capping, and labeling.
Investing in fully automated systems can lower labor costs and greatly increase our production capacity. Maintenance and Safety Considerations for Aerosol Filling Equipment To guarantee the longevity and optimum performance of aerosol filling equipment, proper maintenance is necessary. Routine maintenance & inspections assist in spotting possible problems before they become expensive malfunctions. We ought to set up a regular maintenance program that covers lubrication, cleaning, and replacing worn-out components. Also, monitoring performance trends and pinpointing areas for improvement can be facilitated by maintaining thorough records of maintenance operations. Safe operation of aerosol filling equipment is another crucial factor.
The use of pressurized containers carries inherent risks, such as the possibility of leaks or explosions if improperly handled. It is imperative that all operators receive safety protocol training & comprehend the proper way to operate the equipment. The risks connected with aerosol filling operations can be further reduced by putting safety precautions like adequate ventilation, fire suppression systems, and personal protective equipment (PPE) into place. How to Increase Efficiency with Aerosol Filling Equipment We should concentrate on a few crucial tactics to increase the efficiency of our aerosol filling equipment production.
We must prioritize investing in the comprehensive training of our operators. Proficient staff members are better able to spot possible problems during the filling process and run equipment more efficiently. Our staff can stay informed about new technologies & aerosol filling best practices by attending regular training sessions. We ought to think about incorporating lean manufacturing concepts into our production procedures as well. We can improve productivity and streamline processes by examining workflows & locating wasteful or inefficient areas.
Using just-in-time inventory techniques or rearranging workstations to improve workflow could lower storage expenses & cut down on production delays. To sum up, any manufacturer trying to streamline their production procedures must have a thorough understanding of aerosol filling device. When selecting equipment, we can make well-informed decisions that support our operational objectives by taking into account variables like product type and production capacity. The advantages of effective aerosol filling equipment go beyond increased output; they also include lower costs & better product quality.
Our needs can be met by a variety of equipment types, ranging from fully automatic systems to semi-automatic ones. Also, putting maintenance and safety first guarantees that our business operations function efficiently while lowering the risks connected to aerosol products. Lastly, we can increase the efficiency of our production by implementing lean manufacturing concepts and funding operator training. It is evident as we work through the difficulties of aerosol filling that a calculated approach will result in notable gains in output and financial gain.
If you are interested in learning more about bag-on-valve technology, check out this informative article on what bag-on-valve is. This innovative technology is just one of the many solutions offered by Terco when it comes to aerosol filling equipment. For more information on how Terco can help elevate your production with cutting-edge solutions, be sure to read their article on aerosol filling equipment. Stay up to date with the latest news and updates from Terco by visiting their news page.
FAQs
What is aerosol filling equipment?
Aerosol filling equipment is machinery used in the manufacturing process of aerosol products. It is designed to fill aerosol containers with various types of products such as paints, adhesives, pharmaceuticals, and personal care products.
How does aerosol filling equipment work?
Aerosol filling equipment typically consists of a filling machine, propellant filling machine, crimping machine, and other auxiliary equipment. The filling machine fills the product into the aerosol container, the propellant filling machine adds the propellant, and the crimping machine seals the container.
What are the different types of aerosol filling equipment?
There are various types of aerosol filling equipment available, including semi-automatic and fully automatic filling machines, propellant filling machines, crimping machines, and other auxiliary equipment such as valve inserters and leak testers.
What are the benefits of using aerosol filling equipment?
Aerosol filling equipment offers several benefits, including increased production efficiency, precise filling accuracy, reduced product waste, and improved product quality and consistency.
What industries use aerosol filling equipment?
Aerosol filling equipment is used in a wide range of industries, including the automotive, household, personal care, pharmaceutical, and industrial sectors. It is used to fill aerosol containers with products such as paints, lubricants, air fresheners, and medical sprays.
What are the key considerations when choosing aerosol filling equipment?
When choosing aerosol filling equipment, key considerations include the type of product to be filled, production capacity requirements, filling accuracy, container size and type, and regulatory compliance with industry standards and regulations.
Revolutionizing Aerosol Packaging with Bag on Valve Technology
An important development in the packaging & dispensing of aerosol products is Bag on Valve (BOV) technology. With this novel system, the product to be dispensed is contained in a canister that holds a flexible bag. The propellant, which usually takes the form of compressed gas, is kept apart from the bag.
Key Takeaways
- Bag on Valve (BoV) technology is a packaging system where the product is placed in a bag and the bag is then placed in a can with a valve and propellant system.
- Advantages of BoV technology include longer shelf life, better product protection, 360-degree dispensing, and the ability to use eco-friendly propellants.
- BoV technology has a wide range of applications including pharmaceuticals, cosmetics, food products, and household chemicals.
- BoV technology has a positive environmental impact due to reduced propellant use, lower product waste, and recyclable components.
- Future developments in BoV technology may include advancements in barrier materials, propellant alternatives, and improved dispensing systems.
- In conclusion, BoV technology offers numerous benefits and has the potential for further innovation and sustainability in the future.
The product is forced out of the bag and through the nozzle by the propellant’s pressure when the valve is opened, enabling a precise & effective dispensing procedure. In addition to improving product integrity, this design guarantees that the contents are delivered free of propellant contamination. BOV technology was first developed in response to the demand for safer and more efficient aerosol delivery systems.
Traditional aerosol cans frequently have problems like product deterioration from air or propellant exposure, which lowers shelf life and efficacy. These problems are resolved by BOV technology, which maintains the quality of the formulation by forming a barrier between the product and the propellant. The use of BOV technology has expanded throughout a number of industries, including food products, pharmaceuticals, and personal care, as consumer preferences shift toward more eco-friendly and user-friendly packaging options. maintaining delicate formulations.
The ability of Bag on Valve technology to preserve product integrity is one of its main benefits. BOV systems avoid chemical reactions that might jeopardize the formulation by separating the product from the propellant. For delicate goods like medications and cosmetics, where stability and effectiveness are critical, this is especially important.
Benefits of Bag on Valve Technology | Statistics |
---|---|
Increased Product Shelf Life | Up to 100% longer shelf life compared to traditional aerosol packaging |
Eco-Friendly | Reduced propellant use by up to 100% |
Improved Spray Control | Consistent and controlled dispensing of product |
Reduced Contamination Risk | Separation of product and propellant reduces contamination risk |
Dispensing formulations with versatility. Using BOV technology, a variety of formulations, including foam, liquid spray, and thick cream, can be dispensed. Because of its versatility, manufacturers seeking to innovate their product lines find it to be a compelling choice. Improved Usability & Decreased Waste.
Compared to conventional aerosol systems, BOV systems can offer a more reliable spray pattern & dosage control. Because customers can dispense precisely what they need without overspraying, this accuracy not only improves the user experience but also lowers waste. Numerous industries have adopted bag-on-valve technology, demonstrating its adaptability & efficiency. BOV systems are frequently utilized for products like moisturizers, hair sprays, and deodorants in the personal care sector. For instance, well-known companies have incorporated BOV technology into their aerosol sunscreens, which enables uniform application without sacrificing the stability of the formulation.
Usability is further improved by the ability to dispense products at any angle, which makes it simpler for customers to apply products in difficult-to-reach places. BOV technology is being used more and more in the pharmaceutical industry to deliver drugs in aerosol form. This technology helps inhalers and topical sprays because it guarantees that the active ingredients stay pure and functional until they are used. For example, BOV-enabled asthma inhalers can deliver accurate dosages without compromising the drug’s potency.
Also, this technology is being investigated for use in veterinary settings, where it can safely and effectively administer drugs to animals. In today’s market, the environmental effects of packaging technologies are becoming more and more significant. Compared to conventional aerosol systems, bag on valve technology has a number of environmentally beneficial benefits. The potential for lower propellant consumption is among its most noteworthy advantages.
BOV systems help reduce greenhouse gas emissions because they use nitrogen or compressed air rather than hydrofluorocarbons (HFCs). This change is consistent with worldwide initiatives to phase out dangerous chemicals that fuel climate change. Also, because BOV technology has an effective dispensing mechanism, it frequently leads to less product waste. Conventional aerosol cans may produce needless waste by leaving behind residual product that cannot be dispensed. On the other hand, BOV systems maximize usage and reduce waste by enabling users to remove almost all of the product from the container.
The sustainability profile of many BOV systems is further improved by the fact that they are made of recyclable materials. By appealing to this growing demographic, brands implementing BOV technology may find themselves at a competitive advantage as consumers grow more environmentally conscious. Bag on Valve technology is constantly changing along with industries.
Enhancing user experience and increasing application possibilities are probably going to be the main goals of future developments. Materials science advancements could result in even more resilient and adaptable bag designs that can support a wider variety of formulations or endure greater pressures. New product categories that weren’t previously possible with conventional aerosol systems may be made possible by this. Also, improvements in automation and manufacturing techniques may simplify production and lower BOV system expenses. By incorporating smart technologies into BOV production, businesses can increase efficiency and optimize their supply chains, which could result in notable improvements in consistency and quality control.
Also, continued research into compostable or biodegradable materials for BOV systems may become a crucial area of focus as regulatory pressures regarding environmental sustainability increase. With its many benefits that address consumer demands & environmental concerns, bag on valve technology is at the forefront of aerosol packaging innovation. BOV systems will probably continue to grow in popularity across a range of industries as sustainability and product integrity become more and more important.
Because BOV technology can reduce waste while maintaining product quality, it is a good option for manufacturers who want to improve their products. In terms of the future, Bag on Valve technology looks bright. We can anticipate even more efficiency and adaptability from these systems as materials science & manufacturing techniques continue to advance. BOV technology will probably be crucial in determining how aerosol packaging develops in the future as consumer preferences continue to shift toward more environmentally friendly options. Bag on Valve technology will continue to be vital and relevant in order to satisfy the needs of both modern industries and consumers thanks to the combination of innovation and environmental responsibility.
If you are interested in learning more about bag-on-valve aerosol technology, you may want to check out this article on bag-on-valve aerosol from Terco. This innovative packaging solution offers numerous benefits for products such as cosmetics, pharmaceuticals, and food items. By separating the product from the propellant, bag-on-valve technology helps to extend shelf life, improve product stability, and enhance overall user experience. To complement this technology, Terco also offers gripper water bath and aerosol can filler machines to streamline the production process.
FAQs
What is a bag on valve aerosol?
A bag on valve aerosol is a type of aerosol packaging system that consists of a bag containing the product, which is placed inside a canister. The product is dispensed through a valve system, which separates the product from the propellant, ensuring that the product remains uncontaminated and free from contact with the propellant.
How does a bag on valve aerosol work?
In a bag on valve aerosol system, the product is filled into a flexible bag that is placed inside the canister. The propellant is then filled into the space between the bag and the canister. When the valve is actuated, the propellant forces the product out of the bag and through the valve, allowing for controlled dispensing of the product.
What are the advantages of using a bag on valve aerosol?
Some of the advantages of using a bag on valve aerosol system include: – Longer shelf life for the product – Reduced risk of contamination – Ability to dispense products in any position, even upside down – Environmentally friendly, as it uses less propellant and allows for complete product evacuation
What products can be packaged using a bag on valve aerosol system?
A wide range of products can be packaged using a bag on valve aerosol system, including: – Pharmaceuticals – Cosmetics – Personal care products – Food products – Household and industrial products
What is bag on valve?
Bag-on-valve (BOV) is a packaging technology that allows for the dispensing of liquid and semi-liquid products in an aerosol can. The main component of a Bag-on-valve system is a flexible bag made of plastic, which is placed inside a metal can. The bag is separated from the propellant by a valve.
When the valve is actuated, the propellant, which is typically a compressed gas such as air or nitrogen, pushes the product out of the bag and through the valve. The product is then dispensed into the air as a fine mist or spray. Because the product is contained in a separate bag, it is not in direct contact with the propellant, which reduces the risk of contamination and allows for a longer shelf life.
BOV technology is commonly used for dispensing personal care products such as hair spray, sunscreen, and insect repellent. It is also used for food products like whipped cream, cooking sprays, and salad dressings.
One of the main advantages of BOV technology is that it allows for more consistent and controlled dispensing of the product compared to traditional aerosol cans. Because the product is not in direct contact with the propellant, the amount of product dispensed is not affected by changes in temperature or pressure. This means that the product is dispensed at a consistent rate, which is especially important for products that are used in precise applications like hair styling or cooking.
Another advantage of BOV is that it is more environmentally friendly than traditional aerosol cans. The metal cans used in BOV systems are recyclable and the flexible bags are made of plastic which can be also recycled.
In summary, Bag-on-valve is a packaging technology that allows for the dispensing of liquid and semi-liquid products in an aerosol can, with a flexible bag inside the can to separate the product from the propellant. This allows for consistent and controlled dispensing of the product and also it’s an environmentally friendly solution.
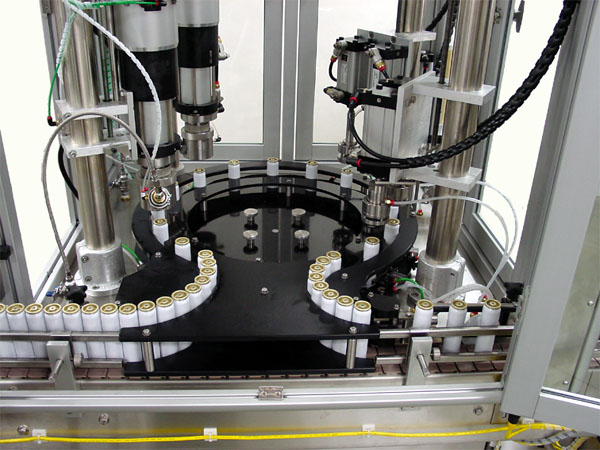
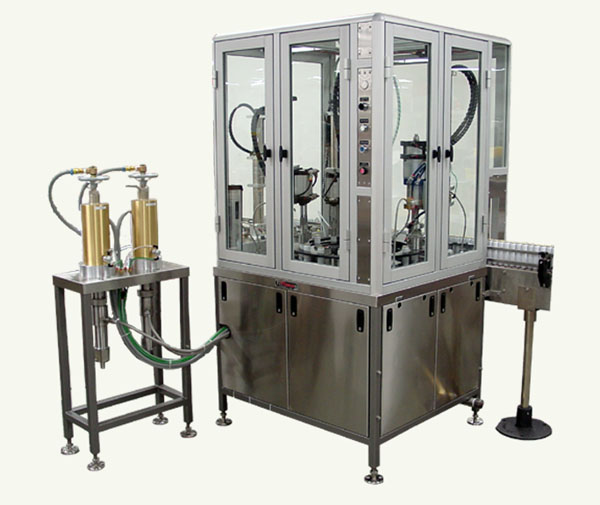
Innovative Packaging Solution: The Bag on Valve Aerosol Filling Machine
The bag on valve aerosol filling machine is a revolutionary method for packaging products with propellant, creating airtight seals between the product pouch and aerosol valve. This unique system allows for clean, hygienic, and leak-free dispensing.
Parts and Operational Concept Of BoV Machines
The product reservoir, the propellant gas chamber, the valve crimping system, and the nozzle are some of the key parts of the bag-on-valve aerosol filling machine.
These devices operate on the basis of the product being placed inside a flexible bag and sealing it hermetically. The bag is enclosed in a rigid aerosol can with a valve attached to the top.
Strict safety and quality requirements are met by the bag on the valve filling machine.
Types of Bag on Valve Aerosol Filling Machines
There are three types of bag on valve aerosol filling machines to choose from, depending on your production scale and requirements.
- Manual filling machines, ideal for small-scale production, involve manual loading and sealing of bags.
- Semi-automatic filling machines are suitable for medium-sized production lines, automating some processes while still requiring human operators for specific tasks.
- Fully automatic filling machines are designed for high-volume production, fully automating the entire filling process from bag insertion to valve crimping.
Choose Efficiency and Quality with the Bag on Valve Aerosol Filling Machine
Armed with this information, select the perfect bag on valve aerosol filling machine for your specific needs and ensure top-notch packaging for your valuable product. Let this innovative technology take your packaging to the next level.
Suppliers of the Bag on Valve Filling Machine
Several distinguished manufacturers offer cutting-edge bag-on valve-filling machines with advanced technology and innovative features. Some notable suppliers include Terco, Inc. renowned for their dependable and efficient systems.
Manufacturers gain a competitive edge by offering products with better user experiences, longer shelf lives, and environmentally friendly packaging. Adopting this innovative technology creates new opportunities for a variety of industries, including pharmaceuticals and cosmetics. It ensures optimal product protection and precise, controlled dispensing. Choosing an automatic, semi-automated, or manual bag on valve filling machine is just one option for the bag on valve approach, which provides packaging solutions that are both customer-focused and sustainable.
Contact Terco about Your Bag on Valve Needs
Can You Spot The Bag On Valve Spray Can Technology?
A ground-breaking innovation in the aerosol product industry is Bag on Valve (BoV). This creative use of spray packaging is revolutionizing the way we use commonplace products, such as household cleaners and personal care items. Can you recognize a BoV product when you see one, though? Let’s look into the realm of bag on valve technology and examine its advantages, uses, and the reasons why both manufacturers and consumers are starting to favor it over other traditional aerosol can-filling technology.
What Does Bag on Valve Mean?
In aerosol cans, Bag on Valve technology is a novel packaging method that keeps the product and propellant apart. BoV employs a flexible bag inside the can to hold the product, as opposed to conventional aerosol packaging, which mixes the product with the propellant. The area between the bag and the can wall contains the propellant. The propellant expands when the actuator is pressed, squeezing the bag and releasing the product through the valve.
Bag on Valve Benefits
BoV technology offers several noteworthy benefits.
- Environmental friendliness: By using nitrogen or compressed air as propellants, BoV systems can reduce their reliance on hazardous chemicals.
- Product integrity: The purity and uncontaminated nature of the contents are guaranteed by the separation of the product and propellant.
- Total evacuation: Customers can use almost all of the product, which minimizes waste.
- Uniform spray performance is ensured throughout the product’s life by the system, which keeps up pressure until the very last drop.
- Spraying in multiple positions: BoV cans function well at any angle, even when turned upside down.
- Increased shelf life: The product is shielded from oxidation and contamination by the hermetically sealed bag.
- Safety: The likelihood of mishaps is decreased by the non-flammable propellants utilized in BoV systems.
Never Fall for Other Spray Products’ Tricks
Even though BoV technology has many advantages, not all spray products on the market make use of this cutting-edge system. Although conventional aerosol cans may have a similar exterior, they do not have the benefits of BoV. Here’s how to distinguish between the two:
- Examine the label: The packaging of many BoV products prominently features the company’s technology.
- Look at the spray: BoV products usually result in a more uniform, finer mist.
- Apply from various angles: BoV sprays function well in any orientation, but conventional aerosols might have trouble when inverted.
- Feel the temperature: Because the propellant doesn’t mix with the product, BoV cans frequently feel less cold when sprayed continuously.
- Pay close attention: Compared to the more abrasive noise made by conventional aerosols, BoV sprays frequently make a softer sound.
Examples of Spray Can Filling Bag on Valve Products:
BoV technology is used in a wide range of products and industries.
Pharmaceutical products: The sterile environment that BoV provides is beneficial for topical medications, wound care solutions, and nasal sprays.
Personal care products: BoV is used in sunscreens, hair sprays, and deodorants because it can dispense the product in a fine mist without the need for chemical propellants.
Food products: BoV’s capacity to guarantee product freshness and reliable dispensing is utilized by whipped cream and cooking sprays.
Cleaners for the home: The spray angle and uniform application of the system make it ideal for use with fabric refreshers and all-purpose cleaners.
Industrial products: BoV is used in paints and lubricants because it dispenses products accurately and completely.
In summary
Spray packaging has advanced significantly thanks to Bag on Valve technology. It is a better option for many applications due to its advantages for manufacturers, consumers, and the environment. Look for BoV products as you browse the aisles of your neighborhood store; they’ll probably improve user satisfaction while being less harmful to the environment.
Customers can make better decisions about the things they buy and use on a daily basis by being more knowledgeable about BoV products and how to choose them. We may anticipate even more cutting-edge uses for this technology in the future, further altering the aerosol packaging industry, as demand for it rises. Thus, consider this the next time you grab a spray can: Is it a bag on valve spray can?
Written as a service by Evolution Point, a Chicago Marketing Agency.
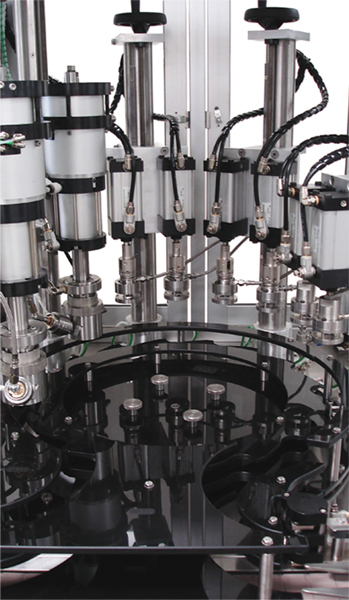
How To Choose Aerosol Filling Companies
Are you considering hiring aerosol filling companies to assist with the machine installation and design for filling your products? The quality, effectiveness, and commercial success of your product can all be greatly impacted by your choice of company. All aerosol products—household cleansers, cosmetics, or industrial solutions—need to be carefully formulated and packaged. Here is a thorough guide to assist you in making this crucial decision.
Related Articles:
- Skill and Knowledge
The key is experience. Businesses with a long history of aerosol filling have accumulated a wealth of knowledge in a variety of product categories and strong problem-solving techniques. When assessing a potential partner, take into account how long they have been in business and their experience with products similar to yours. Their specialized knowledge can assist you in streamlining the production process and avoiding common pitfalls. - Compliance and Quality Assurance
Ensuring quality is crucial. Comprehensive quality control systems should be possessed by a trustworthy aerosol filling company. Seek for certifications such as ISO 9001, which attest to compliance with global quality management standards. Make sure they abide by all applicable national and international laws. The EPA for household products and the FDA for personal care products are two examples. - Technological Abilities
The aerosol filling company’s technology has a big impact on the effectiveness and quality of their output. Among the benefits of contemporary, automated filling lines are consistency, decreased waste, and quicker turnaround times. Ask about the company’s filling technology types, capacities, and handling capabilities for various formulations and packaging styles.
Customization of the aerosol filling process is essential. Should you require particular propellants, fill volumes, or unique packaging designs, the company ought to be able to customize their services to meet your requirements. Another crucial factor is production volume flexibility. The business must be able to adjust its operations to meet your needs, whether they are for large-scale distribution or small batches for specialized markets. This flexibility guarantees that they can satisfy your needs no matter how they change over time. - Support for Formulation and R&D
Having assistance with formulation and research and development (R&D) can be a game-changer for businesses creating new products. Before starting large-scale production, some aerosol filling companies assist clients in developing and testing new formulations to make sure they are safe and effective. With this support, you can refine your product under the guidance of experts and save a significant amount of time and money. Additionally, it guarantees that the finished product satisfies all requirements and performs admirably in the marketplace. - Support for Logistics and Supply Chain
Timely production and distribution depend on effective supply chain management and logistical assistance. A reputable aerosol filling business should have solid connections with propellant, packaging, and raw material suppliers. In addition, they ought to provide logistical services like distribution, inventory control, and warehousing. This reduces delays and disturbances and guarantees a smooth production to market process. Maintaining lead times and product availability through effective logistics is essential for upholding customer satisfaction and competitiveness in the market. - Communication and Customer Service
A successful partnership requires excellent customer service and effective communication. When it comes to handling any problems or concerns that may come up, the aerosol filling company should be prompt, open, and proactive. A dedicated account manager, open channels of communication for feedback, and regular updates on production status can all greatly improve your experience. Good customer service builds a cooperative and happy relationship by guaranteeing that any problems are promptly fixed and that you are always aware of the status of your project. - Standing and Evaluations
Lastly, find out how the business is known in the sector. Seek endorsements and reviews from other companies that have collaborated with them. It’s more likely that a business that has a solid reputation for dependability, quality, and customer service will live up to your expectations. A company’s standing and performance may also be indicated by accolades and recognitions from the industry. A well-known business will probably be more reliable and competent, giving you faith in their ability to meet your needs.
Selecting the best aerosol filling business involves assessing their background, skills, and working methods. You can guarantee a partnership that produces high-quality products effectively and economically by concentrating on elements like quality assurance, technological prowess, customization options, and customer service. Maintaining a strong market presence and achieving product success require this meticulous selection process. In the long run, a successful and seamless production experience can be achieved by taking the time to carefully evaluate possible partners.
Bag On Valve Technology Shows Outstanding Advantages
The market has witnessed a rapid growth of Bag on Valve (BOV) technology these years, especially in the field of pharmaceutics, personal care, and household care.
Other Articles You Might Be Interested In:
Bag on valve technology shows its outstanding advantages in many aspects. It can isolate the product from the propellant gas, thus prolonging the shelf life dramatically. It uses non-flammable gas(Nitrogen or compressed air) as the propellant gas, which is much safer than the traditional aerosol technology. It is also able to eliminate the deterioration of product quality caused by the loss of solvent and decomposition of propellant.
It has been widely used in personal care, household care, food and beverage, pharmaceutics, etc.
The first Bag on valve technology was developed in Japan in the 1990s, and then it got very popular in Asia. It is still expanding rapidly in the European market. As a leader in this field, Nidec-Mitsui developed BOV technology for various industries (pharmaceuticals, cosmetics, etc.) over 10 years. The company based on its own rich experience and latest technologies proposed a wide range of BOV products to satisfy various needs of customers. Nidec-Mitsui’s BOV products are now exported to more than 50 countries/regions around the world with a high reputation among customers for their excellent quality and competitive price.
Pressure-free spray container (PFS) is a new type of spray container which has two parts: the bottle and the cap. The bottle is made of high-quality transparent material, such as polypropylene(PP), polyethylene(PE), polystyrene(PS), or polycarbonate (PC). The cap has a valve for controlling the spray direction. It is pressurized by air or nitrogen, which makes the liquid inside it be sprayed out through the valve. This kind of spray container can be used in all kinds of applications that are normally carried out with aerosol cans, such as household care products, personal care products, food products, etc. Thanks to its pressure-free design and other unique features, it offers many advantages over traditional aerosol cans.
Bag on Valve technology provides an excellent solution to many issues regarding aerosols. It eliminates all problems related to conventional aerosols. See Terco’s superior implementation of Bag on Valve BOV aerosol machines.